Water in an engine can rob it of performance and cause damage if not rectified. Now let’s think of the equivalent in terms of your maintenance system. Your CMMS/EAM is the data engine for your maintenance operations and the single source of truth for maintenance information. How well will that engine perform if you fuel it with watered down data? Water in this instance comes from the inaccurate, incomplete, and in some cases untimely work results entered into your CMMS/EAM from work orders written on paper forms. Data collection can be very difficult if you’re relying on paper forms instead of an app that automatically collects this data for you. Add to that the lost paper orders, and work requests which go unrecorded, and your “fuel” could become very diluted.
There are multiple ways that an app surpasses paper forms. For now, let us contemplate a comparison of paper and mobile processes for maintenance and repair work execution. We need to make some basic assumptions about your maintenance operations to get started.
First, we assume your maintenance organization is digital, at least to the extent of using a CMMS/EAM system. Your organization has made a significant investment in this solution and understands the immediate and long term value of maintenance execution information for reliability, process improvement, and decision making purposes.
Second, your maintenance team uses paper form work orders today which are printed, distributed, assigned, completed, collected, entered into your CMMS/EAM, and then filed and stored per company policy.
Finally, your company is constantly striving to improve maintenance practices, reduce downtime, eliminate errors, and ultimately reduce costs. These are common goals among most maintenance organizations, irrespective of industry, or function (i.e., it’s of interest to asset management, field service, facilities maintenance, etc.).
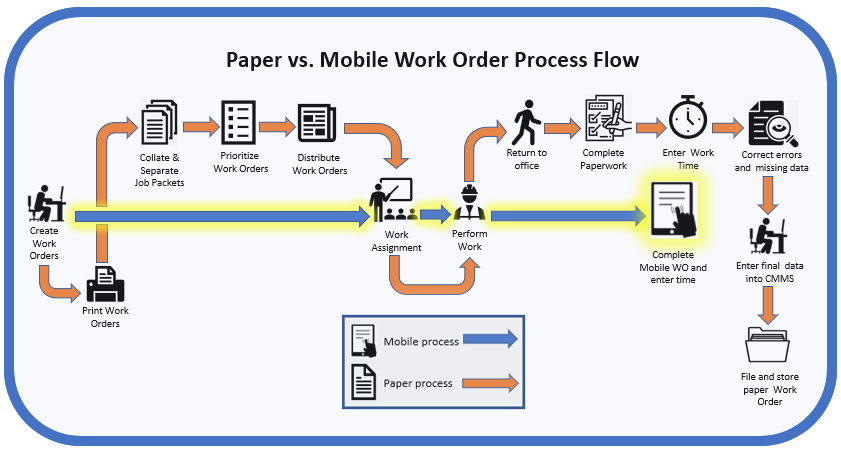
A comparison of typical work processes in both mobile and paper. As you can see, mobile processes typically reduce the number of steps. This reduces both costs and the chances for errors to be introduced.
The example above shows a comparison of typical work processes. Your process, mobile or paper, may have fewer steps, or additional steps, based upon the way your company operates.
The point to be stressed is that mobile work management generally reduces the number of steps, the number of people handling work orders, processing time, and therefore reduces costs. Buying a tablet, smart phone, or other electronic devices to run the app on will certainly carry a cost, but this may be relatively minor. Remember, you’re also going to save a bundle on printing costs.
However, the benefits of mobile over paper extend well beyond just process and costs. Mobile, if properly implemented, can be transformative for the maintenance team. Some of the advantages are obvious and others require more thought.
Let’s start by asking the primary question about going paperless: Who does mobile work management serve? The answer is, the workers first, supervisors and managers second, and finally the maintenance organization as a whole. Remember this if you decide to embark upon a mobile solution.
The mobile application must be built to make the job of conducting and recording maintenance work as easy as possible. This will help to ensure that workers will actually use the application. We can total up pros and cons all day, but that won’t mean anything if no one uses the app. For more information on this, please see Fogg Behavior Model. Beyond being easy to use, the solution should provide additional value in order to achieve the desired behavior by the worker.
Paper Vs. Mobile: Value to the Maintenance Worker
Mobile isn’t valuable unless it offers significant worker benefits over the print process. Asset data look up including failure/work history or adding and viewing of photos, meter readings, manuals, drawings, signatures, other attachments, and parts can all be done quickly and easily from a mobile application without wading through a stack of print documents.
The work order completion process itself becomes a guided experience to assist new users and a quick predictable process for seasoned maintenance workers. Workers can change the status of work orders, notifying schedulers and supervisors, of conditions which restrict work completion, i.e., asset in use, parts, tools, or special equipment not available, etc.
Bar codes can be scanned to note start and completion time, parts used on work orders, or to record inspection points. Test equipment can be directly connected to the mobile device so that reading are recorded without manual entry.
Value to the Supervisor and Manager
With print orders, maintenance supervisors and managers can’t study what is happening during a given shift until work results are recorded. To solve this, you can either have workers report job status by radio or phone, have them enter each order as completed, or enter results at points during the shift. All of these methods take time that could be better spent on executing work orders.
Pen and paper data sources, including work orders, will lead to more frequent errors than with a mobile app.
With mobile, ALL work execution information is reported when the mobile order is completed and may be available immediately, depending upon network connectivity. As long as the data has been synced, it should be immediately available on the supervisor’s screen. Additionally, work order assignment can be displayed on the screen by priority sequence, requiring supervisor approval to work them out of sequence.
Completing work orders, at the work site, contributes to more accurate and complete work results. The mobile workflow requires certain fields to be completed and can provide drop down lists for critical data requirements such as problem, cause and resolution codes. Field editing rules assure that the right data goes into the right fields to satisfy the completion requirements.
Work orders can be pushed out to workers’ mobile devices, eliminating the need to return to an office to pick up new work. Work requests from the field can be easily captured and either completed or sent to supervisors for future assignment. The point here is to capture more work rather than making repairs without documentation, waiting for the paperwork to be produced, or adding the time and materials to an existing work order.
Value to the Organization
For the organization as a whole, mobile provides a more efficient, lower cost process. Paper usage is greatly reduced, helping to meet “green” initiatives. Data quality and depth are greatly improved which support better reliability program data.
Costly calculation errors are reduced or eliminated, and workers spend more time at the assets rather than sitting down in an office to enter work results.
Productivity increases, the organization has a better picture of worker performance, and can compare individual or craft performance for training purposes.
Finally, writing notes becomes much easier. This means the notes on each work order are more likely to provide complete information.
So Why Not Mobile?
For many, like me, the drawbacks of paper work orders seem obvious. With that said, why are so many maintenance teams still using paper for work execution? Some reasons I have heard include:
“Our environment is too harsh for mobile” – I doubt that. Yes, some environments are harsh due to chemicals, temperature, processes, weather, etc. However, if humans can work there, you can likely find a device which will survive in your environment.
“It’s a matter of cost and ROI” – It always is! Contact us if you want help building your business case. You can also read our eBook, "Your Asset Management and Mobility Strategy" for more information.
“Management won’t support the project” – This usually speaks to ROI, cited above, or not effectively conveying the benefits for the organization to management. Again, Prometheus Group can assist you with presentation materials to build a compelling case for Mobile.
“We deployed a mobile solution before, and it failed” – The question is, why did it fail? Beyond that, what steps were taken to overcome the issues with the solution? You need clear objectives for the project, an assessment of current technology, involvement from maintenance workers, supervisors, mangers, IT and others to ensure a successful project and user acceptance.
“Our techs don’t seem to want it” – Talk to as many workers as possible and get their candid input. Are their concerns justified? Make sure they understand what the benefits are for them, before explaining the benefits for the company. It’s usually easier to get people to back something if it appeals to their own interests.
No matter how robust your engine is, it will not run properly if you insist on pouring water in the gas tank. Replacing an inefficient paper process with an efficient mobile solution will help ensure that your engine keeps humming along.
For more information on how Prometheus Group can help you fuel your maintenance processes, please get in touch with us.