Predictive maintenance (PdM) is transforming industries, helping organizations optimize performance, reduce downtime, and enhance asset reliability. As technologies like AI, IoT, and real-time data processing evolve, PdM is entering an exciting era of innovation.
At the forefront of this transformation is I-care, Europe’s leading provider of asset health management solutions. Since 2004, I-care has specialized in advanced strategies like vibration analysis, lubricant analysis, and infrared thermography, completing over 200 successful projects with a team of 150 engineers.
In this article, Cosme Somogyi, R&D Project Manager at I-care, shares his insights on the evolution of predictive maintenance. From digitization and Industry 4.0 technologies to the importance of standards like ISO 55000, Cosme offers an in-depth look at the challenges and innovations shaping the field today
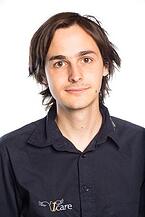
Why Predictive Maintenance Matters in Modern Industry
Predictive maintenance is experiencing unprecedented growth worldwide, driven by advancements in Industry 4.0 technologies, the integration of IoT sensors, and an increased focus on operational efficiency. By proactively identifying and addressing potential equipment issues, businesses can reduce costly downtime, optimize resources, and extend the lifespan of critical assets.
The numbers tell the story of its rising importance:
- The global predictive maintenance market is projected to grow from USD 10.6 billion in 2024 to USD 47.8 billion in 2029, at a CAGR of 35.1%
- Europe leads the charge in adoption, particularly in manufacturing, automotive, and energy sectors, as companies leverage predictive strategies to stay competitive in a highly automated landscape
- According to a report from the US Department of Energy, implementing a robust PdM program can deliver:
- A tenfold ROI
- A 70% reduction in equipment breakdowns
- Downtime decreased by 35%-45%
- Maintenance costs lowered by 25%-30%
These statistics underscore why predictive maintenance is no longer just an option but a business-critical strategy. Particularly in regions like EMEA, where cost efficiency and reliability are paramount, companies are turning to PdM to scale operations and maintain a competitive edge.
Current Trends and Challenges in Predictive Maintenance
Predictive maintenance is shaped by regional practices, industry trends, and emerging challenges. To better understand the current landscape, Cosme discussed with us the nuances of maintenance practices across continents and the broader trends impacting the field.
Key Regional Differences in Maintenance Practices
Q: I-care serves clients on different continents. What are some differences in maintenance practices between Europe and North America?
A: While general practices are similar, cultural differences exist. For example, U.S. companies value local after-sales support, while Europeans prioritize competitive pricing. European companies also tend to work with multiple providers to find cost-effective solutions, while U.S. companies are more loyal to established market leaders. Additionally, standards adherence is more uniform in the U.S., and technical diversity is more prominent in Europe.
Emerging Trends in Maintenance and Reliability
Q: What are the general trends in maintenance and reliability? How has the industry evolved in the last 10-15 years?
A: Trends include consistent data collection, wireless devices, data standards, new sensor technologies, improved security, and NoSQL databases for maintenance data management. Over the years, predictive maintenance has shifted from being a high-end service to a widely accepted key to improvement. Reliability projects have increased, but demonstrating short-term ROI remains a challenge. Improving Overall Equipment Effectiveness (OEE) and reducing maintenance costs are becoming critical in a competitive landscape.
Key Technologies Transforming Predictive Maintenance
Predictive maintenance is at the heart of industrial transformation, leveraging cutting-edge technologies to optimize performance and reliability. From IoT sensors to AI-driven analytics, these innovations are enabling organizations to predict failures, reduce downtime, and improve efficiency. Here's a closer look at the technologies shaping the future of PdM.
IoT Sensors and Real-Time Monitoring
IoT (Internet of Things) sensors are revolutionizing maintenance by providing real-time data on critical equipment parameters such as vibration, temperature, and energy usage.
- Centralized monitoring: Cloud platforms enable organizations to monitor assets across multiple locations from a single interface.
- Proactive alerts: IoT devices help detect anomalies early, allowing maintenance teams to address issues before they escalate.
The Role of AI and Machine Learning in Predictive Maintenance
AI and machine learning (ML) are transforming PdM by enabling proactive, data-driven maintenance strategies.
- Failure prediction: ML models analyze historical and real-time data to identify patterns, continuously improving failure detection accuracy.
- Dynamic scheduling: AI optimizes maintenance schedules based on equipment health, reducing unnecessary interventions and minimizing downtime.
AI-driven insights enable proactive failure detection and dynamic scheduling. ML models continuously improve failure prediction accuracy, enhancing reliability and reducing downtime.
Augmented and Virtual Reality Integration
AR and VR are bridging the gap between digital insights and hands-on maintenance practices:
- Augmented reality (AR): Delivers real-time diagnostics and step-by-step instructions, helping technicians perform repairs efficiently and with fewer errors.
- Virtual reality (VR): Creates immersive training environments, enabling technicians to practice complex procedures in a risk-free setting.
Human-AI Collaboration
The synergy between human expertise and AI is unlocking new possibilities in maintenance strategies:
- AI-assisted diagnostics: Real-time alerts and actionable insights for prioritizing tasks
- Augmented decision-making: Humans contextualize AI insights to align with business goals
- Advanced training: AI tools, coupled with AR and VR, empower technicians with advanced skills
This collaboration ensures that the precision of AI complements human intuition, creating more effective and efficient maintenance workflows.
Technology and Digitization in Predictive Maintenance
Q: How is technology playing a part in the adoption and trends of maintenance and reliability? More specifically, what’s the impact of the emerging digitization of industry?
A: Technology is key to improving maintenance at all levels. Some of the most prominent technologies that we use include dedicated sensors for data collection, automated solutions for data processing, and new wireless sensors for remote diagnosis. We also use corporate analytics and analytics for calculating KPIs (Key Performance Indicators) for all levels of an organization. Industry 4.0 and the ongoing digitization of industry bring together several of the above technologies as a means of providing a virtual control room for maintenance.
Standards and Best Practices in Predictive Maintenance
Adopting and adhering to international standards is critical for ensuring consistency, improving operational efficiency, and reducing risks in predictive maintenance. Standards like ISO 55000 provide a structured framework for asset management, aligning processes with global best practices.
Why ISO 55000 is Essential for Asset Management
Q: What’s the added value and importance of standards in your work in general and of the ISO 55000 standard for managing physical assets in particular?
A: ISO standards ensure alignment to industry best practices and state-of-the-art technologies. For example, ISO 18436 enables reliability engineers to analyze data consistently, while ISO 55000 facilitates dynamic asset management systems. The ultimate goal is to improve OEE and reduce costs while managing risks.
Tips to Implement ISO 55000 in Your Organization
Q: Could you describe how to use ISO 55000 in practice?
A: First, prepare a plan-do-check-act loop, ensuring management support and stakeholder acceptance. Then, implement priority actions and perform regular assessments. Managing ISO 55000 is similar to other systems like ISO 9001 and ISO 14001, requiring resource allocation for ongoing improvement.
Q: Does using ISO 55000 involve special training or certifications?
A: Yes, training is necessary for employees in different roles to align viewpoints and mindsets. Certification and external audits can ensure quality and compliance, maintaining a dynamic system.
Business Impacts of Predictive Maintenance
Predictive maintenance offers transformative benefits for organizations, from cost savings to improved operational efficiency. By addressing maintenance needs proactively, businesses can reduce downtime, extend asset lifespan, and optimize resource allocation. However, successful implementation requires overcoming significant barriers.
How Predictive Maintenance Saves Costs and Boosts Efficiency
PdM directly impacts the bottom line through:
- Optimized maintenance schedules that prevent unnecessary interventions
- Lower emergency costs by addressing issues proactively
- Resource allocation focused on critical tasks
Reducing Downtime with Predictive Maintenance
Downtime is one of the most significant costs for any business. IoT sensors and predictive analytics work together to:
- Detect equipment anomalies in real time
- Provide actionable insights to address issues early
- Reduce both the frequency and duration of downtime events
Extending the Lifespan of Equipment with Predictive Maintenance
Proactive maintenance not only prevents unexpected breakdowns but also:
- Addresses minor issues before they escalate into major problems
- Improves the reliability of assets, ensuring consistent performance
- Reduces the need for premature capital expenditures on new equipment
Overcoming Common Barriers in PdM Implementation
Q: Based on your experience, what are the common day-to-day challenges enterprises face when deploying predictive maintenance and reliability solutions?
A: Challenges include lack of early stage reliability planning, resource allocation for measurements and data analysis, and misalignment between production and maintenance. Changing mindsets to view maintenance and production as collaborative rather than competing activities is also critical.
Future Predictions for Predictive Maintenance
The future of PdM is being shaped by rapid technological advancements. From sensors to automation, these innovations are driving the adoption of more efficient and reliable maintenance strategies.
How Technology Is Shaping the Future of Maintenance and Reliability
Q: How is technology playing a part in the adoption and trends of maintenance and reliability?
A: Technology is key, with sensors, automation, wireless devices, corporate analytics, and virtual control rooms driving improvements. Industry 4.0 technologies integrate these advancements, enhancing predictive capabilities.
Predictions for the Next Decade in Predictive Maintenance
According to Cosme Somogyi, the next decade will redefine how industries approach maintenance. Key trends to watch include:
- A shift from curative to predictive strategies: Reactive maintenance will become a thing of the past as organizations fully embrace predictive and proactive approaches.
- Widespread adoption of AI, IoT, and automation: These technologies will play a central role in predictive analytics, failure detection, and dynamic scheduling.
- Integration of advanced management solutions: Seamless operations will be achieved through the adoption of smart platforms that unify data, insights, and execution.
These predictions underscore a transformation in industrial maintenance, where technology and strategy converge to create more resilient, cost-effective operations.
The Strategic Importance of Predictive Maintenance
Predictive maintenance is far more than a technological advancement—it’s a strategic game-changer. By delivering measurable ROI, minimizing downtime, and enhancing asset reliability, PdM empowers organizations to optimize their operations and stay ahead in an increasingly competitive landscape.
As industries embrace the possibilities of Industry 4.0, investing in predictive maintenance is no longer optional—it’s essential. Companies adopting these proactive strategies are not only improving operational efficiency but also gaining a critical edge in scalability, cost savings, and resilience.
Prometheus Group stands at the forefront of this transformation. With a comprehensive suite of predictive maintenance solutions, Prometheus Group empowers organizations to implement cutting-edge strategies that drive results. From IoT sensors and AI-powered analytics to advanced management platforms, Prometheus Group offers the tools you need to unlock the full potential of PdM.
Start transforming your operations today. Explore Prometheus Group’s innovative solutions and discover how we can help your business thrive in the Industry 4.0 era.