What is Condition-Based Monitoring?
Condition-based monitoring (CBM) in maintenance is focused on preventing asset failures, downtime, and unnecessary practices by monitoring asset health to determine what maintenance needs to be completed and when. It can be considered essential to any predictive maintenance strategy. Condition-based monitoring dictates that maintenance should only be performed when certain thresholds are reached, or indicators show signs of decreasing performance or upcoming failure.
Traditionally, monitoring a machine for these thresholds and indicators included non-invasive measurements, visual inspections, performance data and scheduled tests and is completed at pre-set or predetermined intervals. Condition-based monitoring, however, looks at potential failure modes and their indicators, and then monitors for those.
Common types of condition-based monitoring include vibration analysis, vibration monitoring, oil analysis, and temperature tracking. Real-time data is gathered through sensors, providing an ongoing method of testing and tracking asset health. This data can be extremely useful not just for the maintenance department, but for operations staff and fleet managers as well.
Goal of Condition-Based Maintenance
The goal of condition-based maintenance is to spot upcoming equipment failure so maintenance can be proactively scheduled when it is needed – and not before. This is part of what separates predictive maintenance from preventive maintenance.
Preventive maintenance strategies rely on performing certain operations on a particular schedule. The schedule itself can be based either on usage or time, or a combination of both. For example, the schedule may call for an oil change every 10,000 cycles, or for a component to be replaced every six months. This schedule is rigorously followed, regardless of how much life is left in the lubricants or parts.
The philosophy behind predictive maintenance, however, is to only perform those tasks when they’re actually needed to ensure optimal uptime on the equipment. This generally means CBM to ensure that maintenance is triggered when assets meet certain predetermined conditions.
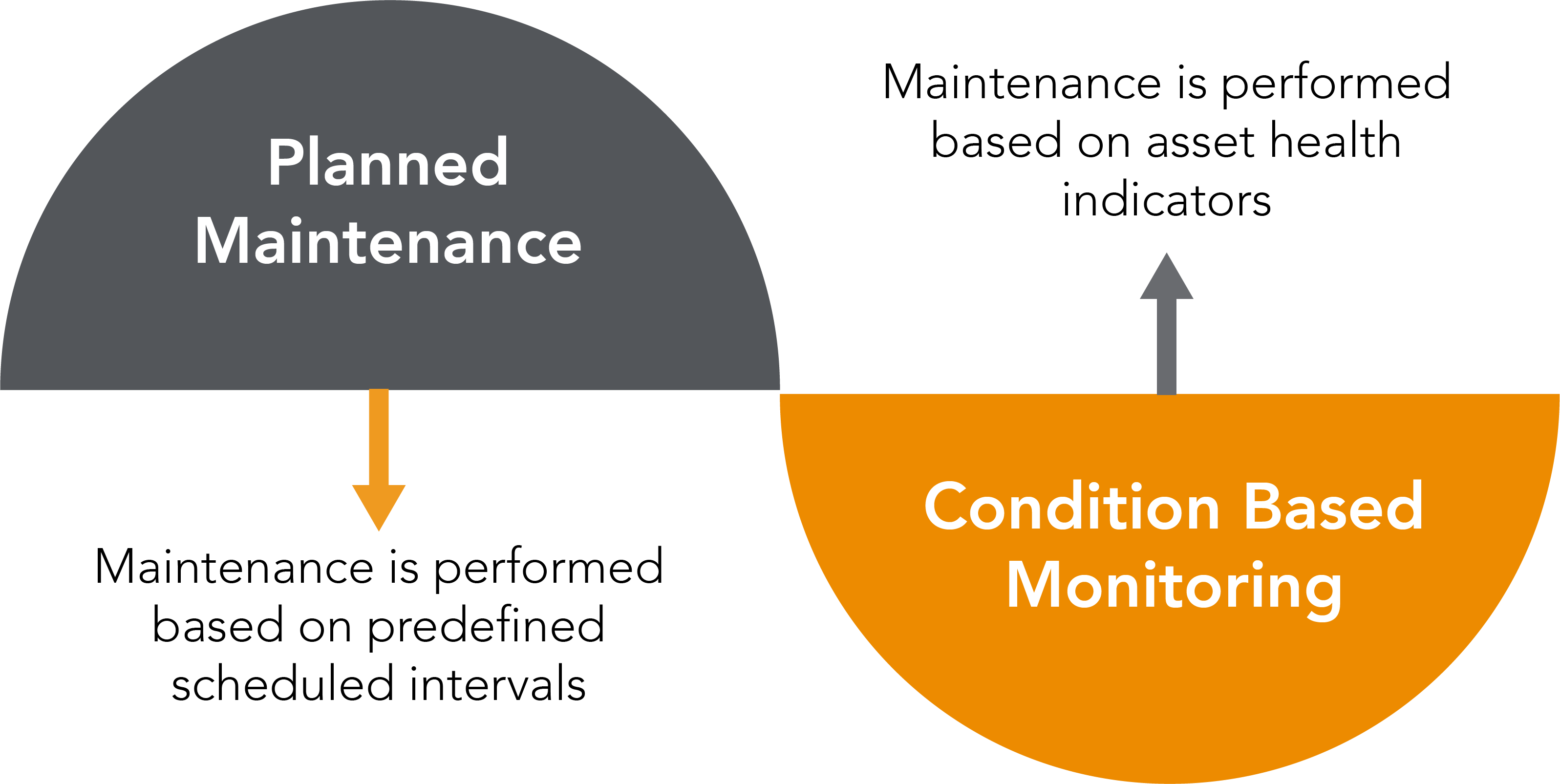
9 Types of Condition Based Monitoring
Common types of condition-based monitoring include vibration analysis and vibration monitoring, oil analysis, and temperature tracking and measurement.
As we noted above, some of the most common types of condition-based monitoring look at vibration, oil, and temperature. However, there are many other methods, including acoustic analysis, motor circuit testing, electrical monitoring, electromagnetic measurement, radiation analysis, and laser interferometry.
Another form of CBM is to look at the equipment’s performance data. A failing asset may suffer degraded performance. This type of degradation may provide clues showing where maintenance is required.
We’ll briefly go over these types of monitoring and some of their applications.
1. Vibration Analysis
The way assets respond to vibration may indicate when and where maintenance is needed. Wear on parts can cause vibrations that can be analyzed to determine developing flaws in components. Vibration analysis includes various techniques, such as shock pulse analysis and broadband vibration analysis. Common applications of vibration analysis are detecting and assessing rotational and structural issues, such as imbalance and misalignment.
2. Oil Analysis
This method relies on testing lubricants and other fluids. Information can be gleaned about the fluid itself as well as the equipment. Tests can be run for wear particles, water contamination, viscosity, and more. Contaminants in lubricants and other fluids may indicate an upcoming failure. Common applications of oil analysis include compressors, gearboxes, and of course throughout the transportation industry.
3. Temperature Measurements
This method includes simple temperature measurements, as well as more advanced techniques that involve passive or active thermography. In thermography, cameras capture heat emitted from assets. An analysis of these images can reveal areas of potential failure, such as worn parts. Excess heat, or any kind of thermal anomaly, is often an indication of some type of problem, such as improper lubrication, worn parts, or misalignment.
4. Acoustic Analysis
You may be able to hear a problem directly, but that isn’t what we’re usually talking about when it comes to acoustic analysis. In maintenance, acoustic analysis can be sorted into two broad categories: sonic and ultrasonic. Sonic analysis is typically conducted with microphones and is used for lubrication analysis, such as determining if part of the equipment isn’t properly lubricated.
Ultrasonic analysis is considerably wider in application. Sonic analysis listens for noises in the human hearing range. Ultrasonic analysis goes beyond this, making it especially useful in areas where there is a lot of audible noise. Sensors can be set to listen for a particular sound that indicates a potential failure, even if the sound is too high-pitched for humans to hear. Common applications include detecting leaks, cavitation, and improperly seated parts.
5. Motor Circuit Analysis
Broadly speaking, motor circuit analysis is used to determine the overall health of a motor. It should not be confused with motor current signature analysis, which only looks at resistance to ground. Motor relies on detecting electrical imbalances and degradation of insulation, as these are the most common causes of motor failure. Motor circuit analysis can be conducted online, while the motor is running, or offline, when the motor is de-energized.
6. Electrical Monitoring
Faults can sometimes be detected by looking at electrical parameters. A number of different characteristics can be tested this way, including induction, pulse and frequency response, capacitance, and resistance. This method often relies on measuring degradation trends in the electrical system, allowing preventative maintenance to occur before the asset fails.
7. Electromagnetic Measurement
This is quite distinct from electrical monitoring, which looks at circuits and their characteristics. Electromagnetic measurements instead measure distortions in the magnetic field and current changes to identify issues. In essence, a field or current is induced either inside the equipment or to its surfaces. Analysis will show where defects are causing disturbances in the field.
8. Radiation Analysis
Broadly similar to the X-rays performed in hospitals, radiation analysis uses radiation imaging to look inside assets and components. This may be one of the most thorough methods of non-destructive testing.
Essentially, radiation analysis looks at the absorption rates of radiation in the material being tested. Internal flaws, such as corrosion, may not be seen with the naked eye. However, these flaws absorb differing amounts of radiation, allowing them to be detected.
9. Laser Interferometry
There’s a place for laser interferometers in any application that demands precision measurements. The technique measures wave displacement of two laser beams, generated using a beam splitter, which can identify defects in both the surface and subsurface of many materials. Laser interferometers can be split into amplitude-splitting and wavefront-splitting.
How IIoT has changed Condition Based Monitoring
Industrial Internet of things (IIoT) has changed the way condition-based monitoring can be completed. Sensors installed on the assets can perform ongoing vibration and oil analysis and monitor temperature changes. This greatly reduces the need for manual inspections and testing. Sensors will monitor the asset condition for indicators of decreasing performance or imminent failure.
When indicators arise, the sensor will notify the maintenance team of the change in asset condition through an IIoT solution. Maintenance teams can respond to the issue and perform the necessary maintenance immediately.
For example, a certain piece of equipment usually vibrates at a given frequency. If that frequency starts to vary, or changes substantially, it could mean something is starting to fail or needs to be replaced. The sensors will register this change and notify the maintenance team of the potential issue so they can respond accordingly.
IIoT and condition-based monitoring allows maintenance teams to anticipate a potential failure and take action. Maintenance teams can take the asset down temporarily to prevent a major failure. It is better to be down for a short time to replace a worn part than to have a failure that requires an unknown amount of downtime.
The application of IIoT technology on condition-based monitoring can reduce maintenance costs by up to 25%, cut unplanned outages by up to 50%, and extend the lives of machines by years.
Advantages of Condition Based Monitoring
One big advantage that Condition Based Monitoring offers is the ability to gain a better understanding of your asset health. Close observation and data analysis of the assets helps plant engineers get to know the unique quirks of each asset.
Condition- based monitoring helps maintenance teams make more informed decisions about performance optimization and maintenance needs. It also gives maintenance and reliability organizations the information they need to improve long-term asset health and to better their maintenance processes and practices.
The overall benefits of condition-based monitoring include:
- Increased uptime/reduced downtime
- Reduction in/elimination of unplanned failures
- Decreased maintenance costs
- Increased asset life
- Reduction in collateral asset damage
- Greater ease in prioritization and planning of work orders
- Increased efficiency in maintenance practices and management
Maintenance activities based on asset condition, rather than on a pre-set interval, has the potential to progress maintenance activities to a new level of efficiency. Monitoring asset health results in fewer failures, which in turn results in improved equipment availability and more efficient operations for longer periods of time.
Maintenance teams are more informed about their assets and can make more confident maintenance decisions. With advance warnings of machine failures, unexpected breakdowns can be avoided with planned repairs, allowing more time to be spent on other priority areas such as asset performance, energy efficiency, production output, and more.
The Role of Prometheus APM in Condition-Based Monitoring (CBM)
Condition-based monitoring (CBM) has become an essential part of modern maintenance strategies, offering businesses a data-driven approach to optimizing asset performance. By focusing on real-time data and predictive insights, CBM helps reduce unplanned downtime, extend asset lifespan, and improve overall operational efficiency. The integration of IIoT technologies has further enhanced CBM, enabling continuous monitoring of key performance indicators such as vibration, temperature, and oil quality.
Prometheus APM is designed to complement and enhance CBM practices by offering advanced tools for real-time monitoring, AI-driven diagnostics, and seamless integration with other systems. By consolidating data from various sources into one centralized platform, Prometheus APM provides maintenance teams with the insights needed to make proactive decisions and prevent equipment failures before they occur. Additionally, its ability to integrate with other enterprise tools ensures a holistic approach to asset performance management, allowing businesses to fully leverage the advantages of CBM and other predictive maintenance strategies.
For industries that rely on complex machinery and critical assets, combining condition-based monitoring with Prometheus APM offers a powerful solution to improve asset reliability, reduce maintenance costs, and drive operational excellence. To learn more, schedule your free, personalized demo today.
Condition-Based Monitoring FAQ
The five elements of condition monitoring are:
- vibration analysis
- oil analysis
- temperature measurements
- acoustic analysis
- motor circuit analysis