Do you have the right spares in stock when your equipment fails? Do you have too many of the wrong spares and need to write off part of your inventory each year? Spares are a requirement, yet a pain for many organizations. Why are they a pain? They typically are not managed with the level of rigor that all other materials groups are, but they need to be.
So where does one start when trying to get their spare parts program organized? Well, any spare parts program is made up of many different aspects. When all aspects are working together, the spare parts program ensures the right spares are available, in the right quantity, at the right time.
Why Are Spares Needed?
Spare parts are kept on site typically for one of two reasons; unexpected failures, and poor work management practices. We can all agree that some failures are unpredictable, and, in those cases, we should have the right spare parts on hand to enable a quick repair.
In other cases, spare parts are stocked to perform routine Preventive Maintenance (PMs) and planned work. If a work management program is in place, and effective, one could argue that the need to stock extra parts can be eliminated.
So, the first step to fixing a spare part program is to ask yourself, why are we stocking this part? Is it because of an unexpected failure, or are we compensating for a poor work management program?
Having The Right Data
Once the reason for stocking the spares has been determined, the right data is needed to ensure that the stock levels are managed correctly, spend leveraged and that there are no duplicate parts in the storeroom. The right data can be broken down into a few specific types;
- Master Data is what allows a spare part to be identified and specified. Master Data includes the description of the spare, which should follow a defined taxonomy, manufacturer, part number, class, sub-class and any attributes.
- Procurement Data is the data that allows the spare part to be procured. Procurement data includes the price, lead time, and vendor.
- Usage Data is the historical data that reflects how often the part has been used in the past and what equipment the parts below to.
All of this data is critical to the management of the spare parts and should be controlled by a governance process to ensure it is accurate and consistent.
Organizing a Storeroom
When you walk into your storeroom, what do you think of? A junk drawer in the kitchen or an auto parts store? The storeroom should be organized in a way that allows easy access to the commonly used parts (think nuts, bolts, Loctite, etc.) and controls access to the more important or expensive parts.
Also, the parts are organized by the class (or type) of parts. You don't have headlights for a car in section and headlights for a truck in another. All lights are in the same section. So why are storerooms constantly organized by machine and not the type of part? This makes parts hard to find and can lead to duplicate parts.
So, when setting up your storeroom, think of your local auto parts storeroom and model your storeroom after the store.
Calculating The Right Level of Spares
Most stocking levels are determined by the craftsman thinking he will need 3 to do a job, so he asks to have six stocked. The storeroom staff then double that min to arrive at a max. As you can imagine, this leads to an extremely high level of extra or unnecessary stock in the storeroom.
How to Calculate Spare Parts Requirements
The right way to calculate the level of spares is to use Data (see above). The min, max, safety stock and criticality can be calculated with a few basic formulas:
Minimum Stock Quantity (Min) = (usage per year / 365) x Lead time
Maximum Stock Quantity (Max) = Minimum quantity + Economic order quantity (EOQ)
Economic Order Quantity = √(2DS/H)
D = Usage per year
S = Ordering cost per order
H = Inventory carrying cost
Safety Stock = (maximum lead time – normal lead time) x normal consumption rate
Normal consumption rate = expected annual usage / 365
Criticality can be determined by using a basic risk matrix:
1 – 2 = Do not stock
3 – 12 = Setup stock
15 – 25 = Setup critical stock
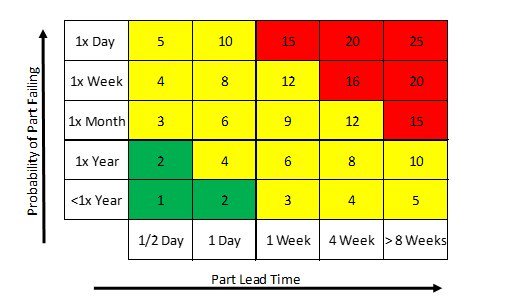
There are much more advanced spares calculation formulas and techniques available, but if most organizations use this basic approach, the savings realized across the storeroom would be tremendous. Data-driven decision-making trumps gut feeling any day.
Shelf Life Management & Maintenance of Spares
Spare parts stock, like most other materials, have a limited shelf life. If that spare parts life is exceeded and the parts are used, it has the potential to impact reliability. Take a V-belt for example. If a V-belt is hung up on a nail and left there for two years in the sunlight, the V-belt will develop a weak spot from hanging on the nail and the rubber will degrade due to the UV light. If this belt is installed, how long will it last?
Spare parts also require maintenance. Yes, you read that right. Take for example large motors, should have their shafts rotated on a regular basis to prevent flat spots from developing on the bearings. If this is not done, the larger motors can be installed with a defect and lead to a premature failure.
The best way to make sure that your spares are preserved in the best possible way is to follow the manufacturer's recommendations. Without any manufacturer's recommendations, the storeroom can follow these basic rules of thumb:
- Keep rubber products out of direct sunlight
- Don't hang belts on a peg or nail, lay them down
- Rotate large motors shafts 1-1/4 turns every 3-6 months
- Use a first-in, first-out approach with stock
- Bearings have a shelf life of 5-8 years (after that the lubricant will dry out)
- Keep the spares in their original packaging to prevent contamination
Keeping spare parts in good condition is not difficult, it just requires a little bit of forethought.
Managing Spares Performance
"You Can't Manage What You Don't Measure," and this is true in the storeroom as well. Do you know what your stock turns or stock-outs are? How much stock hasn't moved in the past 18 months?
When looking at storeroom performance, there are many different aspects to consider, so if you are not currently measuring anything, pick a measure or two to focus on that area. For example, if the craftsmen are complaining that the storeroom never has the right parts, but there is a large amount of stock spare parts in the storeroom, consider looking at stock turns.
However, when picking the proper performance measures, be sure to select a balancing measure as well. If you choose to focus on stock turns to evaluate if you have the right stock, be sure to balance with stock-outs. This way the storeroom is still being managed in a way to deliver service.
Spare Parts Management for Maintenance
Spare parts management for maintenance matters because it directly impacts the efficiency, reliability, and cost-effectiveness of operations. In industries where equipment downtime can lead to significant financial losses or operational delays, having the right parts available at the right time is essential for minimizing interruptions. Effective spare parts management helps ensure that maintenance teams can quickly address issues, extend the life of critical assets, and avoid unplanned breakdowns. It also enables better inventory control, reducing excess stock while preventing shortages that could disrupt operations. Managing spare parts successfully is central to keeping assets running efficiently and maintaining a competitive edge. Consider the following list when evaluating your spare parts maintenance.
- Operational Strategy: A solid operational strategy ensures spare parts management lines up with bigger business goals, helping save time and money. It lays out a clear plan for managing inventory, scheduling maintenance, and keeping assets running smoothly, all of which are key to cutting down on downtime and improving operations.
- Spare Parts Prioritization: Prioritizing spare parts helps focus resources on the most important ones, cutting down on long downtimes and expensive repairs. By knowing which parts are most likely to fail, businesses can keep the right parts in stock and be ready when things break down.
- Leveraging the Right Data: Having accurate, up-to-date data makes it easier to make smart decisions about purchasing, storing, and using spare parts. By looking at past performance and trends, businesses can stay ahead of potential issues instead of reacting to problems as they happen.
- Effective Inventory Control: Good inventory control means you don’t have too many or too few parts, which saves money and makes sure you have what you need when stuff breaks. It’s about keeping an eye on stock levels, predicting future needs, and adjusting orders to keep things balanced.
- Standardizing Work Order Process: Standardizing how work orders are done helps everything run smoothly, speeds up communication, and reduces mistakes. By following the same process for creating and handling work orders, you can make sure spare parts get ordered and used the right way, reducing downtime.
- Understanding Lead-times for Parts: Knowing how long it takes to get parts is crucial for keeping your stock levels right and fixing things on time. If you can plan for delays in getting parts, you’ll avoid waiting around for the right part to show up and keep everything running.
- Calculating Risk for Equipment: Evaluating risks helps you figure out which equipment and parts need the most attention. By identifying high-risk equipment, you can focus on the parts that matter most, avoid unexpected breakdowns, and save money on repairs.
- Stocking Parts for New Equipment: Having parts ready for new equipment ensures you can fix things quickly without waiting. Stocking up on critical parts early means less downtime as new machines come online and keeps everything running smoothly.
- Implementing Security Measures: Keeping spare parts secure stops theft and misuse, making sure they’re available when you need them for repairs. Using things like access controls and tracking systems ensures that valuable parts stay safe and are where they’re supposed to be.
- Optimize Bill of Materials (BOM): Keeping your Bill of Materials (BOM) updated helps you identify the right spare parts and manage inventory better. With an accurate BOM, you avoid ordering the wrong parts and make your maintenance process more efficient, cutting down on waste.
- Utilizing EAM: Enterprise Asset Management (EAM) software brings together spare parts management, maintenance, and asset tracking, making everything run more smoothly. With EAM, you can monitor equipment performance, predict failures, and make sure parts are ready when you need them, reducing downtime and extending asset life.
Gain Control of Your Storeroom With Reliability-Centered Maintenance
While the article above is not an in-depth step by step guide to transforming your storeroom, it should prompt you to think about what could be done differently in your storeroom. I encourage you to pick one of the topics above and think about what changes you can make.
Remember, to find success; you must first solve the problem, then achieve the implementation of the solution, and finally sustain winning results.
Do you want a solution that makes it easier to find the right parts at the right time? Request a demo of our Master Data as a Service solution below.