When health and safety professionals consider their options to modernize their permitting processes, it can be a challenge to sift through the buzzwords and the theory to get a real understanding of how the solution would work on a day-to-day basis at their specific organization.
How does the solution work? What can it do? When does it come into play? Who uses it and when?
To clear up these questions, this is a sample “day in the life” of an organization using Prometheus ePAS as their Integrated Safe System of Work (ISSoW). In it, you will see who uses the solution at each step in the process — but please remember that our solutions are fully configurable, and the Prometheus Group team will be happy to help you set up the solution to work with your goals, personnel permissions, and processes.
Step by Step: Managing Your Permit and Safety Requirements
Let’s begin with “why ePAS?” Prometheus ePAS is so much more than a permit-to-work solution. Rather, ePAS is an integrated control-of-work system, meaning you can manage isolations, risk assessments, and the normal permit-to-work as well. On top of that, ePAS gives you intelligent templates, consistency, and enables configurable standardization of company workflows, while still allowing individual sites to maintain their local language and unique requirements for some jobs.
That is the vision; now, let’s see how that vision becomes a reality.
Step 1: Maintenance Receives a Work Request/Notification
This phase is where the initial requirement for one or more permit(s) arises. No matter how your Work Orders are generated, if there are controlled elements associated with the work, permits are probably required.
As an ISSoW, ePAS connects with your ERP/CMMS system. As you plan your work orders, the critical information the maintenance team inputs is used to generate a detailed and informative permit request so that the operations team is aware of work being planned as early as possible.
ePAS can be configured to allow maintenance planners & schedulers to manually generate permit requests, or this can be automated based on a status of a work order, such as “Scheduled.”
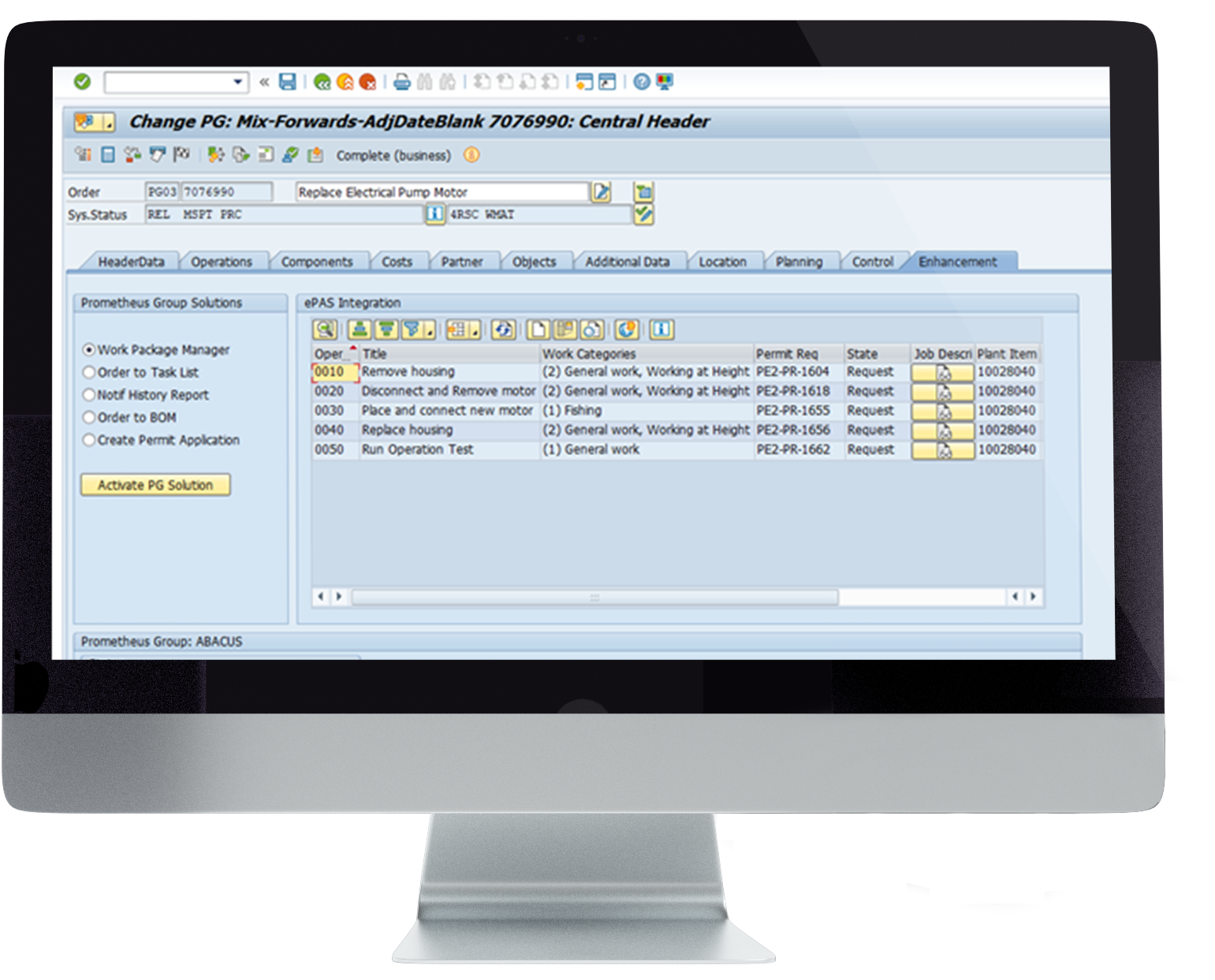
Step 2: Plan the Job
Planning of the permit, or object, starts in step two. This can range from a variety of object types, some of which have been listed below:
- Permit to Work
- Isolation Certificate
- Risk Assessment
- Confined Space
If the permit is being created from scratch, configurable templates can make the planning process simple and reduce the likelihood of mistakes or omissions. Hazards can be outlined along with control elements or other requirements.
If a permit was created from a work order or maintenance plan, these can automatically be tied to templates in ePAS to dramatically streamline the entire process.
Step 3: Site Review
It is imperative to compare the job site to the permit to confirm that all hazards have been identified and will be addressed. What if some hazards were missing on the original permit? Maybe it rained and you can see an area that is now a slip/flood risk. Not a problem. ePAS allows your permit planner to electronically add this information during the site review. ePAS also allows for the capture of images from the job site so information can be shared remotely. In other words, you can have instant feedback from any of your team members and collaborate on the fly! Not to mention, with the digital edition, the permit remains organized and continues to meet the designated requirements or standards even as you change or add information. Gone are the days where a change or addition meant the creation of a whole new permit. ePAS will intelligently align with your business process and assess when changes made need re-review/approval.
This is also where any relevant documentation can be reviewed or attached, or mark-ups be done to piping & instrumentation diagrams (P&ID’s) for example. These will be available for the work party when the permit is issued.
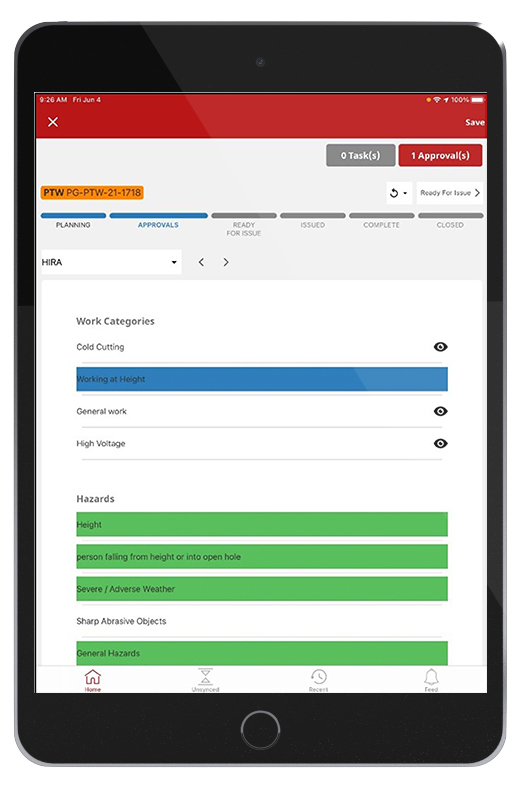
Step 4: Approve the Permit
After checking the permit against the site, you are ready for approvals. The approvals process can be configured to your organization, or even be site specific. Permit approvals are dynamic, and your organization can adjust the approvals process to require more than just the supervisor to sign off, dependent on certain criteria, if you so choose. It is important to remember though, just because the permit is approved, does NOT mean the permit has been issued.
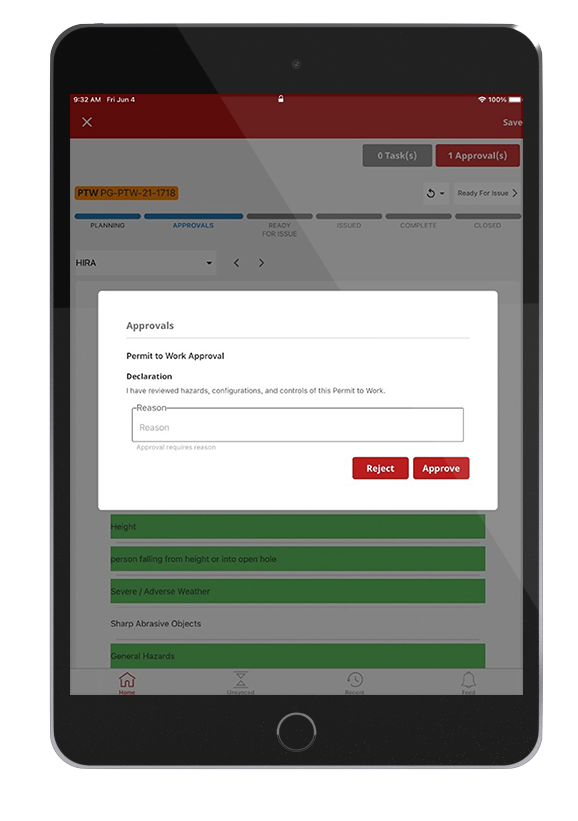
Step 5: Verify & Issue Permit
Even though we have now approved the permit object, work cannot begin until the permit is issued. Before anything else happens, the personal identity of the permit recipient must be verified. This is a simple process that usually involves the scanning of an ID card or presentation of some other ID that can authenticate the person and verify that any necessary certifications and credentials are up to date. Verification of the identity and certifications is important because each certification connects a specific kind of work. For example, an electrician with a high voltage work qualification would not be verified for crane operation without the appropriate credentials, and vice versa. In order to successfully complete the verification process, the identity and certifications of the recipient must match what is listed on the permit. Once the permit has been approved and the recipient has been verified, the permit can be issued, and work can begin!
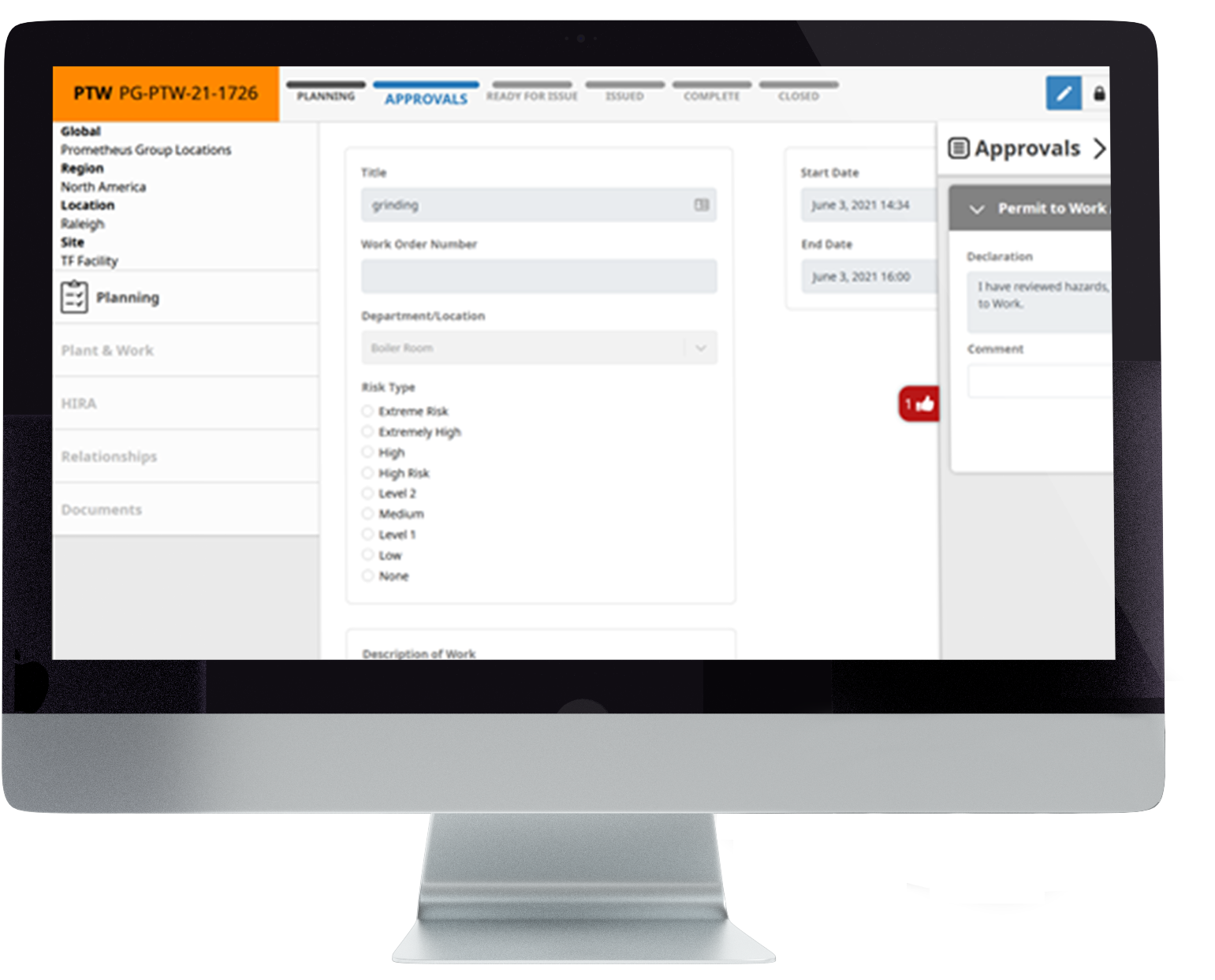
Step 6: Work Party Sign On/Off
If work can begin…why is there another step? As with most jobs, there is no one catch all. The permit holder is likely doing the job with a team, and each individual team member may be required to sign on to the permit. This signing on can be done via paper or digitally, and of course with ePAS, you will receive digital prompts from the “Tool-Box Talk” requesting ID and qualification checks where possible as well as acknowledgements of the hazards and controls associated with the work. Signing on also means signing off and is much of the same in terms of functionality. Sign offs can be done on paper or electronically and will prompt a return permit questionnaire.
The above workflow represents how many of our customers have configured their processes in ePAS. For the majority, just six clear and straightforward steps create an efficient, yet detail-oriented permitting process. One of the items critical to that marriage of efficiency and comprehensiveness is Prometheus Group’s intelligent templating. Our smart templates drastically reduce human error and promote consistency without removing key human elements.
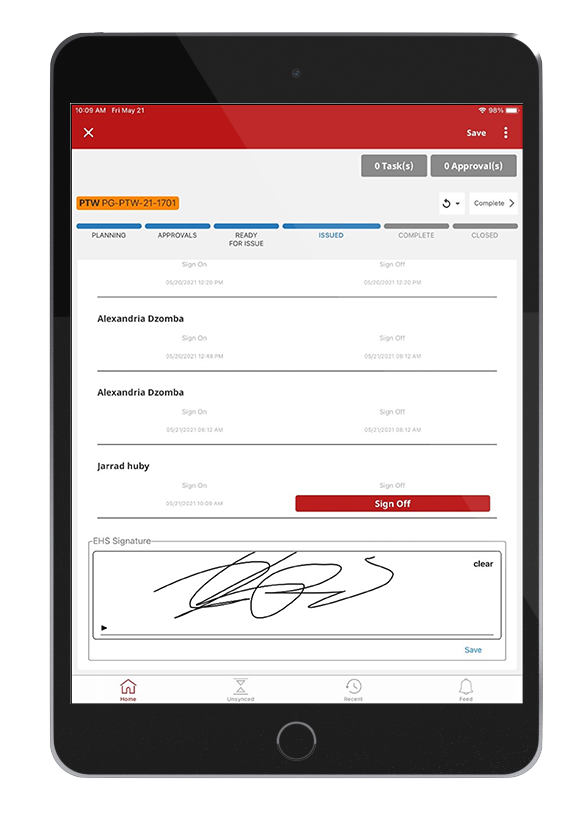
Integration with Your SAP, IBM Maximo, Oracle and Other EAMs
Prometheus ePAS integrates directly with your existing maintenance system, be it SAP, Maximo, Oracle, or any other EAM or ERP system. This integration enhances communications between maintenance and operations and allows for real-time updates across the board. Streamlined information creates a more consistent workflow and data accessibility increases efficiency in permit-to-work, isolation management, risk assessment, and other safety areas.
One of the important things to note is that the ePAS integration is what you make it. Integration does not have to be done fully. One of our customers who chose to do a partial integration. EnergyAustralia, integrated ePAS with their security system as an electronic permit, project, and electronic lock manager. ePAS is recognized for its’ data tracking capabilities, even when partially integrated and not connected to an EAM, ERP, or CMMS, because it keeps the data for life, tracks under flexible authorities, and is highly accurate. Of course, Prometheus ePAS is flexible in its integration abilities and can be configured to meet your organization’s processes and best practices. Whether you want a fully integrated product or a partial integration, Prometheus Group has you covered with ePAS.
Maintenance Mobility: Making Your Permits Remote
In the past two decades, the possibilities for remote work have skyrocketed. Mobile utility work would have been impossible, and travel has always been costly. Today, technology allows for the option of remote site checks, identity verifications and quality assurance. As mentioned in the previous section, ePAS users can remotely check on the quality and condition of field stations from their office, even if that is several states away. Because of the real-time nature of ePAS, management teams do not have to worry about information being obsolete. Updates can be made immediately and can lead to a reduction in company costs.
ePAS mobile brings the field information to a single point and keeps data remain secure while also keeping your team aligned. No more data duplicates or missing pages. ePAS allows for mobile inputs from wherever you are, whether you are online or offline. Utilizing the mobility of ePAS also enhances communication between maintenance and operations. It is important to realize your business goals and find a permit system that suits your business needs. Explore more benefits of going digital with our digital ePAS solution.
Integrated Safe System of Work: Prometheus ePAS
From the easy-to-follow steps to execute a permit, to integration with your existing EAM or ERP, to mobile capabilities, Prometheus ePAS works for your business and safety. The ePAS solution is flexible and makes it easy to manage more than just your permit-to-work safety needs. Check out more on how Prometheus Group can help actualize your milestones with ePAS.